When many people think of spectroscopy, they don’t associate it with the manufacturing of glass; rather, many people recognise spectroscopy as a solution for the pharmaceutical industry. However, spectroscopy is one solution that crosses many disciplines. It is no secret that any manufacturing industry suffers from problems in their quality control and material quantification approaches, and glass manufacturing falls into this category.
For those who don’t know, spectroscopy is a technique used to see how a material reflects, absorbs and generally interacts with light. How the material interacts with this light tells scientists a lot of information about its molecular composition and structure. And just like the production lines in pharmaceutical plants, spectroscopy is a solution of great benefit to the glass industry.
Continuous Monitoring
Continuous monitoring is not the most straightforward procedure for any industry and not many techniques enable continuous monitoring from a quality control point of view. Continuously monitoring a glass production line is a key process, especially when you get down to the molecular level. Whilst many people can see with the human eye if a material is deformed, broken or of poor quality from a bulk perspective, the ability to see defects within the intrinsic structure of the material is significantly more difficult.
Whilst a few defects do not constitute a bad material (and if we’re being picky, all materials contain some molecular sized defects), inefficient packing of molecules or the incorrect composition within the glass is a problem, and one that can comprise the safety of the product. Given that almost all manufactured glass will be used in an environment involving members of the public, ensuring the safety of the glass is of utmost importance.
The use of spectroscopy doesn’t stop there as it extends to coatings on the surface of the glass. Many commercially available products, whether they are used in photovoltaics, phones or in buildings, have some type of coating to protect the surface from damage and degradation. Spectroscopy offers a way to measure if the coating has been deposited uniformly across the surface and can isolate points where there is insufficient coating. Spectrometers can again be used on coating production lines to provide real-time, non-contact monitoring over a wide surface area by measuring multiple points simultaneously.
Spectroscopy offers a much better alternative to current methods that revolve around post-processing inspections. With post-processing inspection methods, if the product is not up to standard, then there is the potential for large amounts of product to be lost as it is often too late to fix any issues. This is negated with real-time spectroscopy monitoring.
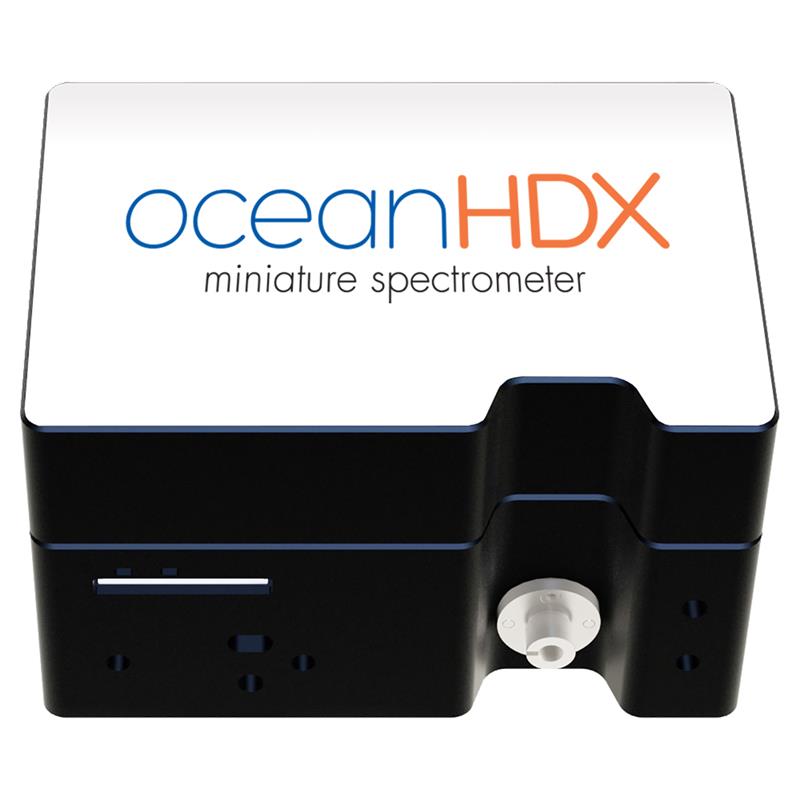
What Do Glass Manufacturers Need?
It goes without saying that manufacturers require a reliable instrument. But with spectroscopy, what exactly is a reliable instrument?
The spectroscopy instrument must be able to provide in-line, real-time monitoring, otherwise the solution is of no greater benefit than other approaches. As with any monitoring and analytical solution, the creation of fast and repeatable results is always a bonus. This is particularly true for long production lines, where downtime can be minimized from accurate measurements.
Reliability is a key factor for many production lines. There are two ways in which an industrial-grade instrument can be reliable. These are a high longevity, otherwise known as a high mean time between failures (MTBF), and a high robustness. Environments where an instrument could be exposed to dirt and other particulate matter can often lead to the frequent replacing of instrument components. For many companies, this disturbance leads to an increase in both downtime and costs.
Manufacturers also want easy to service components. Whilst minimizing the downtime of instruments is a key factor to obtaining high efficiencies, all instruments will require maintenance at some point. When the time comes, components from a reliable source that can be swapped easily enables technicians to minimize downtime and speed up all maintenance protocols.
The Spectroscopy Solution
Founded in 1989 by three oceanographers, Ocean Optics offers a range of spectroscopy solutions that fit the needs of the glass manufacturing industry. One of the most recent examples is the Ocean HDX spectrometer, which provides a high throughput, low stray light and excellent thermal stability for many industrial processes including non-contact, in-line transmission spectroscopy used in glass manufacturing.
Composed of a charge coupled device (CCD) array and high definition optics, Ocean Optics delivers a spectral performance that outstrips the conventional spectrometers on the market today. The versatility is also a testament to the quality that these spectrometers offer and they can even be used with optically dense samples.
The Ocean HDX spectrometer is functional over a wide wavelength range (200-1100 nm) and is stable in processing environments of up to 40 °C. One major benefit for any production line is size, and this spectrometer has a very small footprint. Even though it is compact, its data processing and communication abilities are not, with the software having the capability to accommodate up to 50,000 spectra at any one time.
There are many things that can go wrong on the processing lines of a glass manufacturing plant, but the ability to monitor them and provide a swift and reliable solution with minimal maintenance is the gold standard when it comes to analysis equipment. Spectroscopy is an excellent example of premium analysis equipment, especially when it comes from a reliable source.